ABOUT OUR LEATHER
We are craftspeople and artisans, with a passion for leather. We source only the finest pearl crust in the world, then manufacture it with heart and diligence, to our customers’ exact specifications.
We have complete control over the entire leather-making process.
With more than 50 years of leather manufacturing experience and our beautiful campus of state-of-the-art production facilities, Townsend Leather is able to offer customers an incomparable line of leather services.
Our experienced craftspeople painstakingly inspect and certify excellence at every stage. Every order undergoes extensive and comprehensive testing to guarantee compliance with the highest of industry quality standards for performance and flammability.
Leather Production
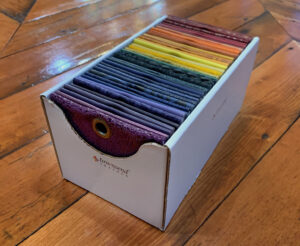
The Townsend Facility
Located in the heart of the Leather-Making Region, Townsend has ready access to the latest developments in leather technology and to a labor force experienced in leather production. Our capital investment in facility improvements and in new state-of-the-art leather manufacturing equipment affirms our commitment to producing high-quality, innovative products.
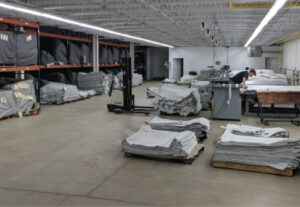
Sourcing
Producing high-quality leather begins with acquiring the best raw materials. At Townsend, we accept only the finest hides and skins from partner tanneries around the world to ensure we are providing our customers with the best yield and value available.
Our leathers begin with the careful selection and control of crust procured from West European Bulls. The hides of these regions are the best in the world in regard to selection which we consider to be crucial in producing the highest quality leather.
West European Bulls are the best due to excellent veterinarian practices, the stable and mild climates of these regions, and the manner in which the animals are allowed to graze in wide-open fields without barbed wire fencing. These animals are not branded (as are animals coming from other parts of the world) and Bulls are raised to a maximum of 18 months old.
While we do not do the tanning ourselves, we are aware of how the tanning process affects the hides we procure, and we only use hide sources that strictly adhere to sound environmental practices. Once we select the hides, they are re-graded to our high-quality standards and to the appropriateness of end product type, then aniline-dyed, processed and finished in our own factory.
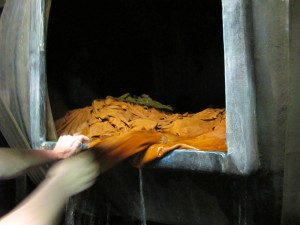
Aniline-Dyeing
Once we have the hides in-house, we use aniline dyes (which are water-based) to custom-color the hides to meet our customers’ specifications. As all hides are unique in their natural markings, the hides also absorb dyes differently from hide to hide and even in different sections of a hide. We drum dye our hides and tumble them in a rotating drum to make sure the dye penetrates the hides as consistently as possible.
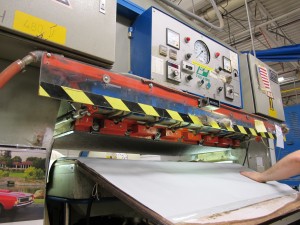
Embossing Patterns and Textures
We have the largest collections of embossing patterns for leather under one roof in the U.S. with over 700 embossing plates and more than 140 calendar rolls. Through the use of specialized techniques by our highly skilled leather craftspeople, many textures can be embossed on whole cowhides without showing overlap lines. This maximizes cutting yield and greatly minimizes the need for excess seams during upholstery.
We have internal graphic design capabilities that allow us to create custom embossing patterns in unprecedented turn-around time.

Hand-tipping and Hand-rubbing
We offer options for unique finish applications, including hand rubs and hand-tipping applications that highlight embossed patterns (Hand-tipping) or the natural grain of the leather (Hand-rubbing). Because the characteristic finish effect is applied by hand, variation within a hide and from hide to hide should be expected as part of the beauty of this leather; each hide is given individual attention and is unique in its beauty. These hands-on capabilities allow us to truly raise our leather to a new level of craftsmanship and artwork.
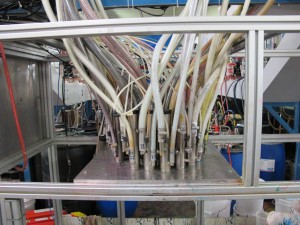
Finishing
Finishing can refer to any enhancing effect applied to leather after it has been tanned. Examples are dyeing, embossing, buffing, antiquing, waxing, waterproofing, and so on.
We most commonly refer to Finishing in terms of our products that have a protective pigment or topcoat applied. Our most popular example is our Classic leather. Classic, and other similar products, are made by a process of surface coating with a mechanical spray application of pigmented formula and topcoat which provides protection from soiling, fading, and wear. Finished leathers have uniform color consistency and there are fewer defects apparent with a Finished Leather as compared to an Aniline Leather.
Quality Control Standards
Every order of Townsend Leather is thoroughly tested in our own laboratory to ensure that it meets or exceeds industry performance standards. In addition to routine quality tests, we are also able to perform many other tests to meet a job’s specifications or submit our leather to an independent laboratory for certification. Because we are the manufacturer, controlling all production processes and retaining the exact formulas and retainer cuttings of each order, we can control dye lot variation and produce previous dye lots to match from year to year.
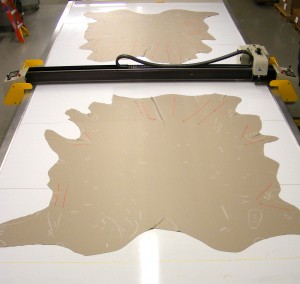
Pattern Cutting
Our high-speed, modular leather cutting system features automated hide scanning, perimeter identification, and flaw recognition. It offers the most advanced cutting and nesting technology available today for improving cutting yield and overall productivity. For customers with repetitive pattern cutting requirements, the Townsend Pattern Cutting System can produce multiple sets cut to your specifications on schedule and at defined costs.
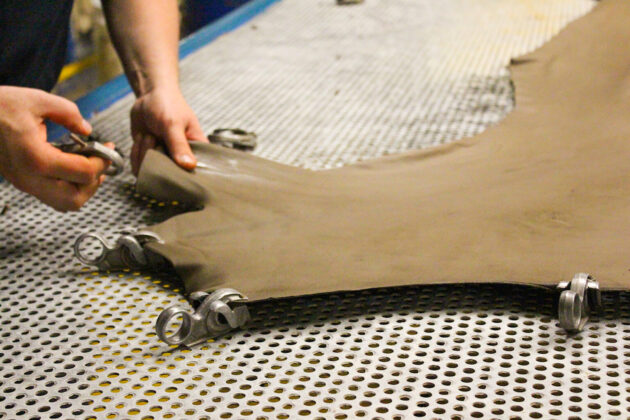

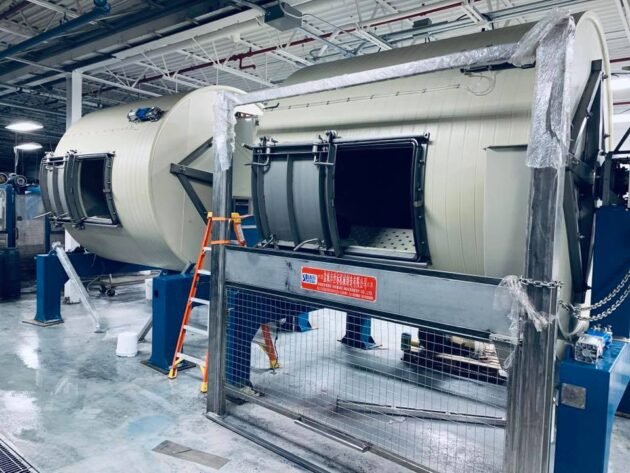
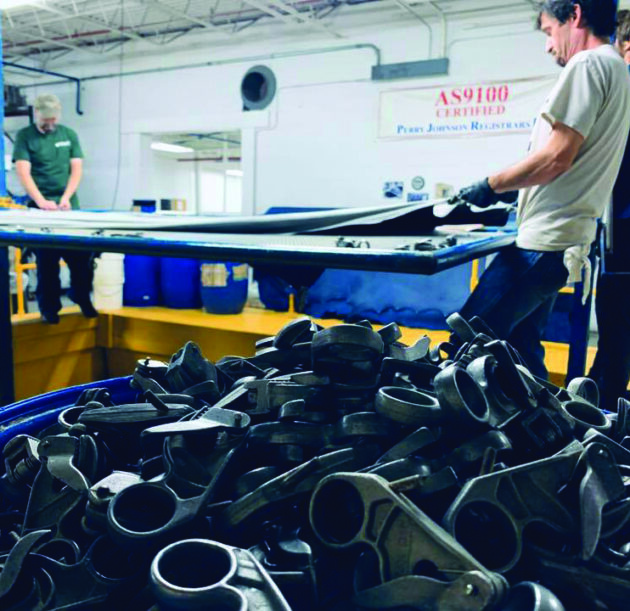
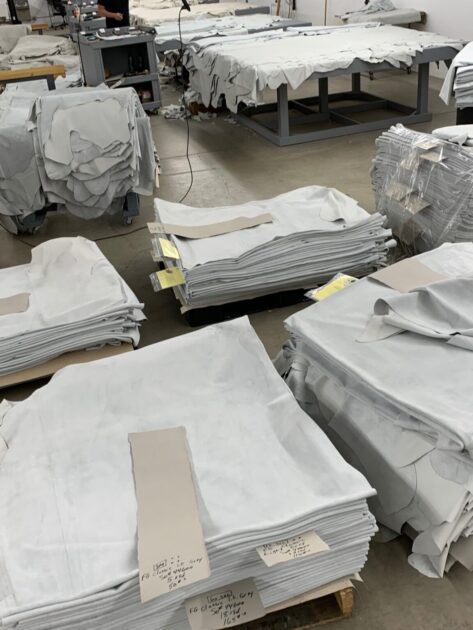
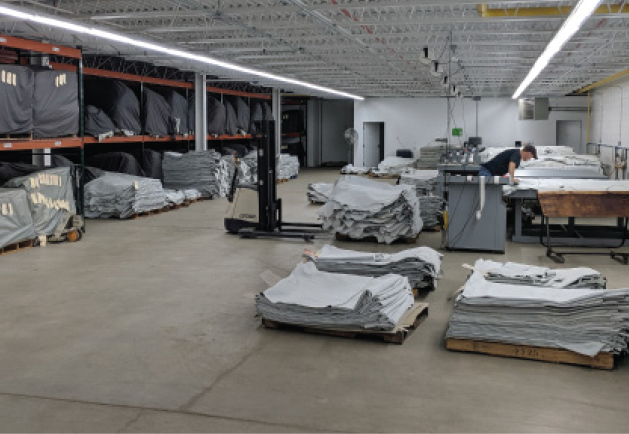
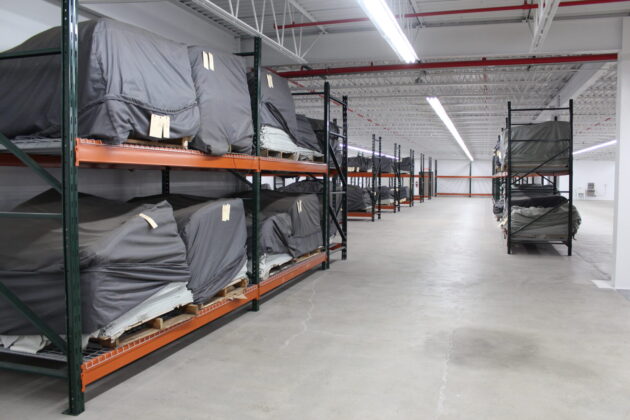
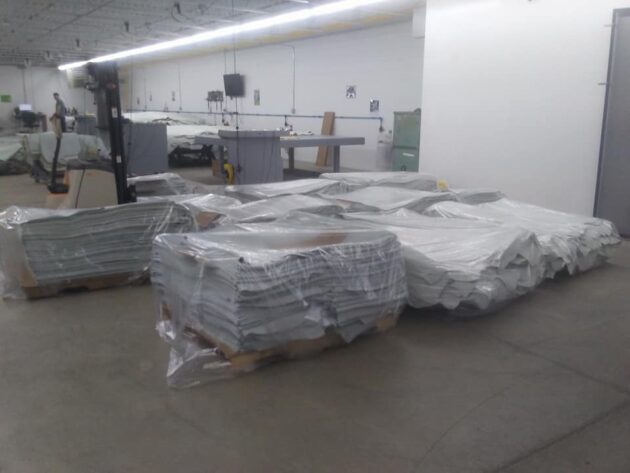
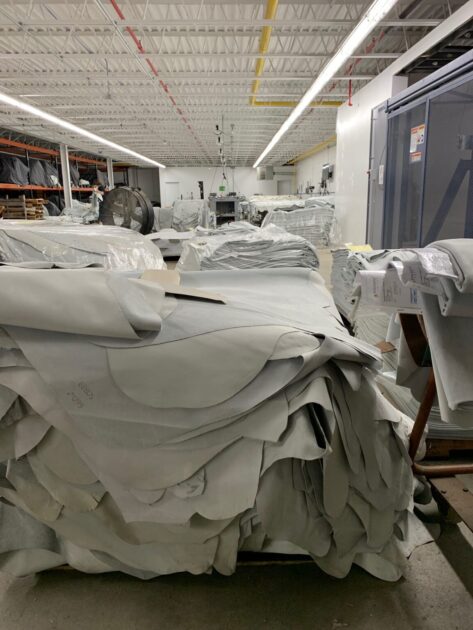
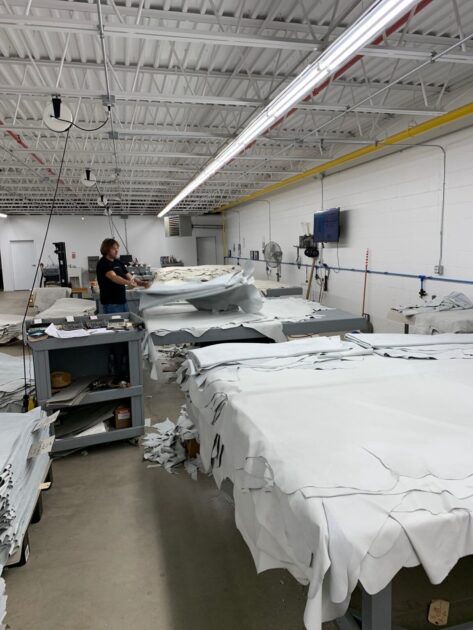
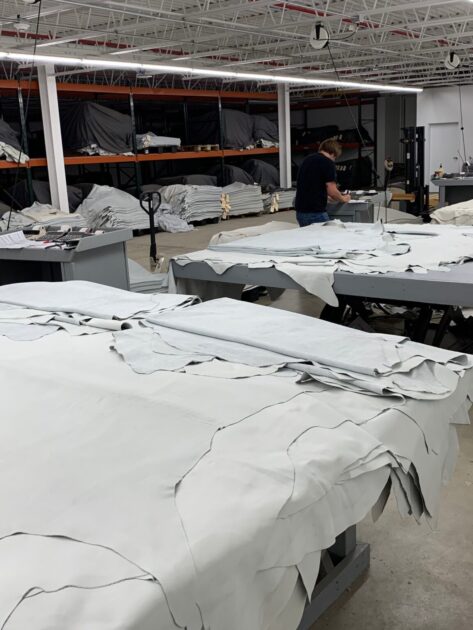
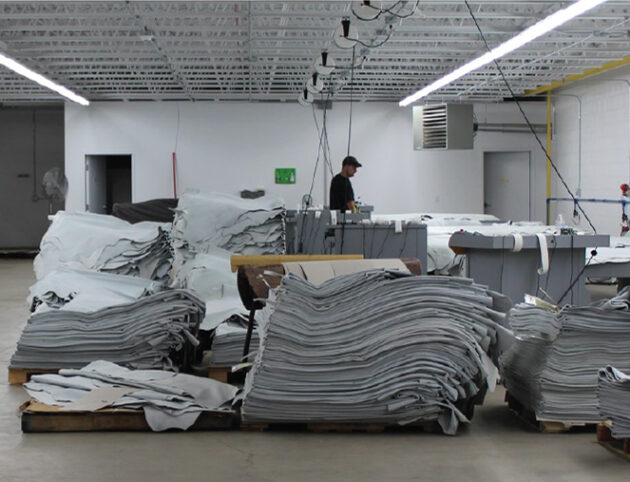
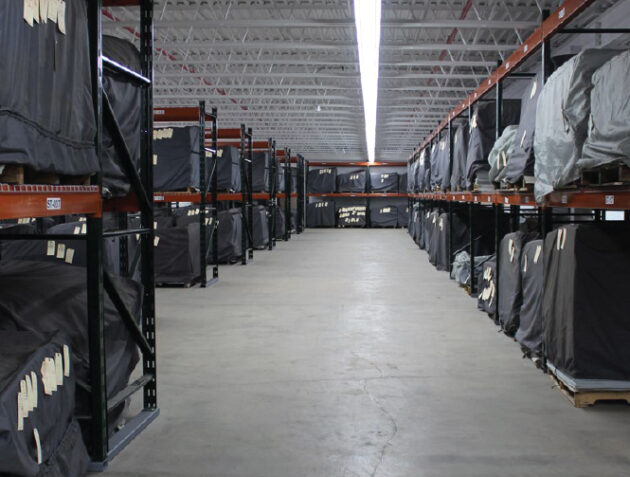
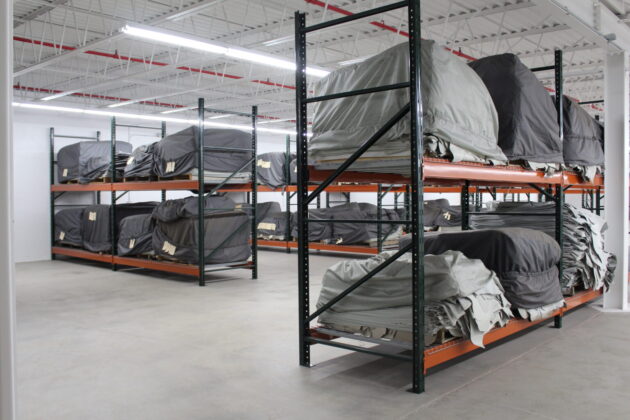
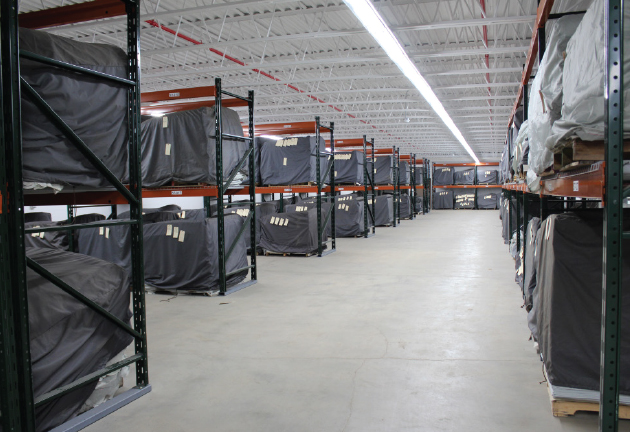
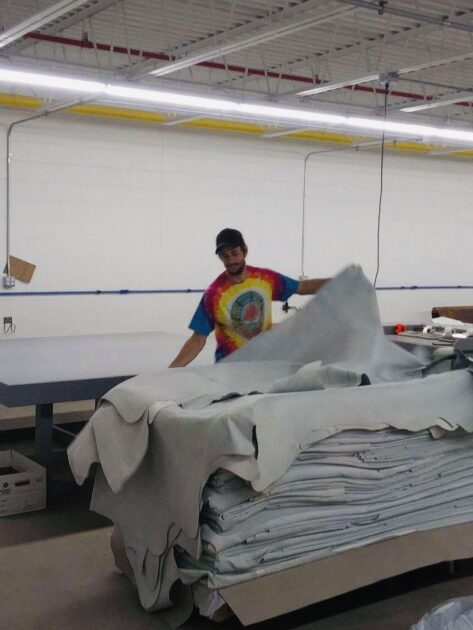

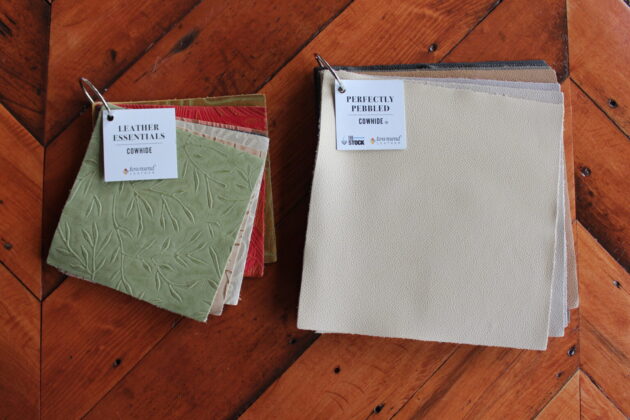
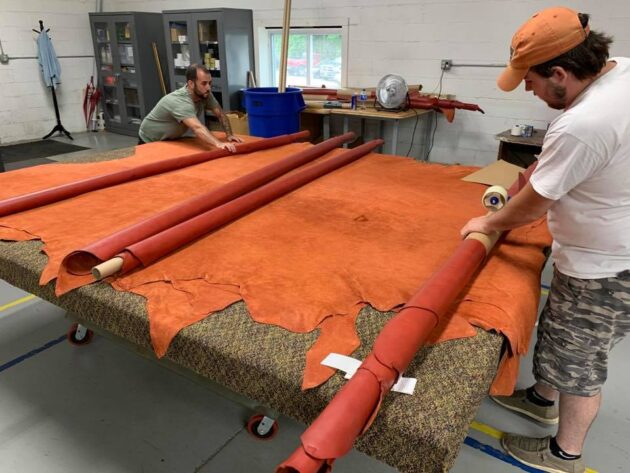
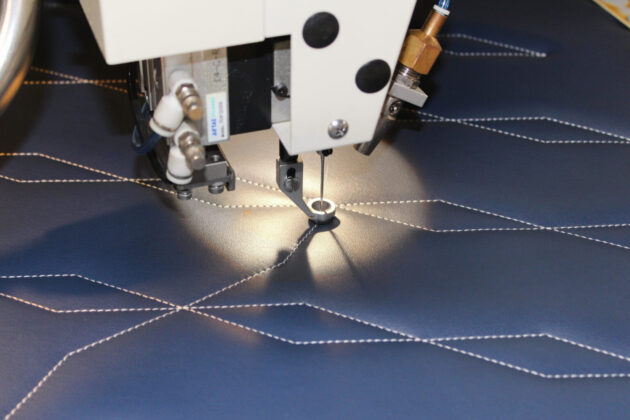
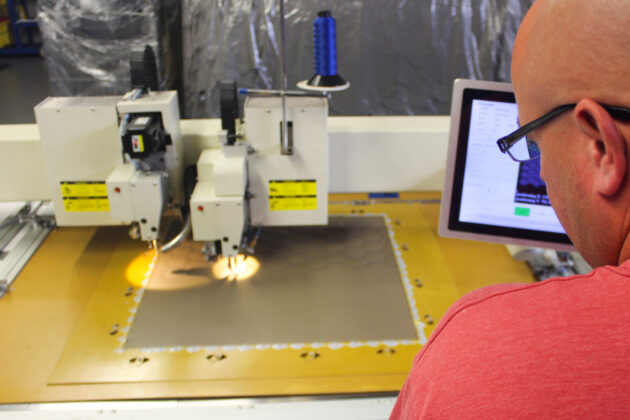
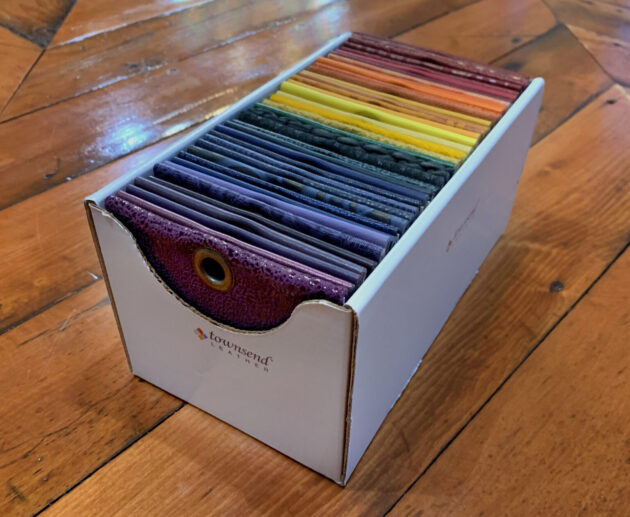
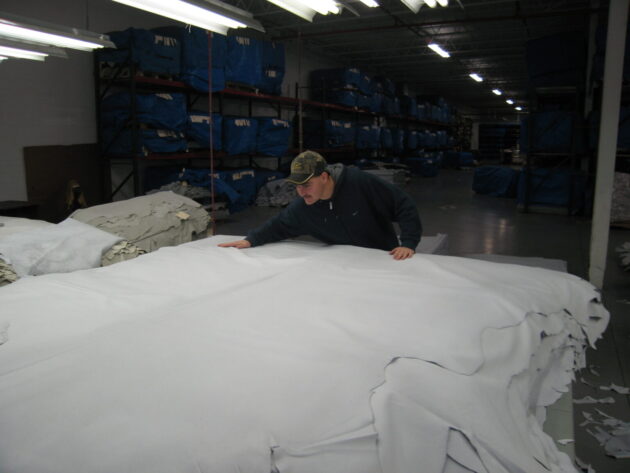
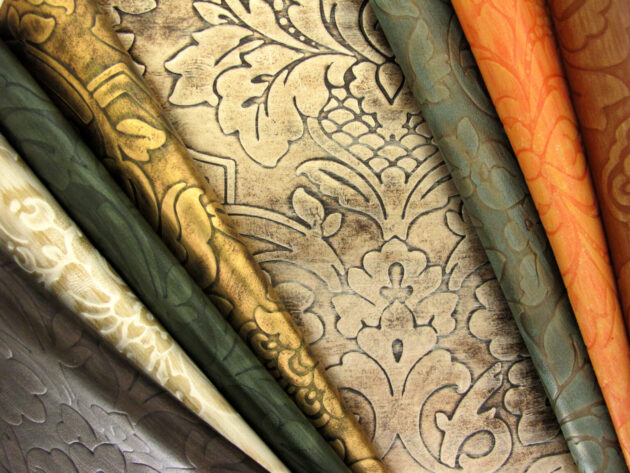
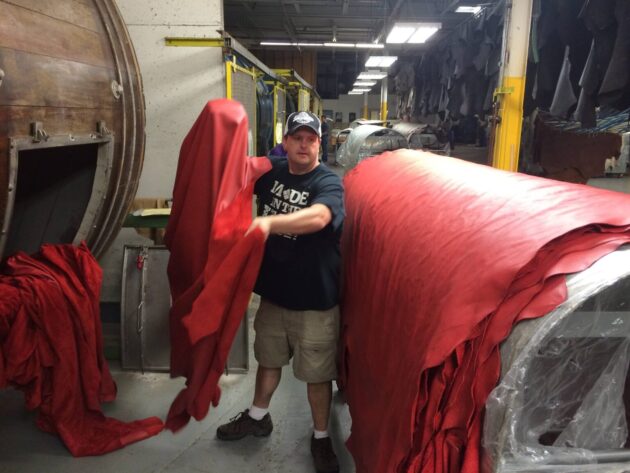
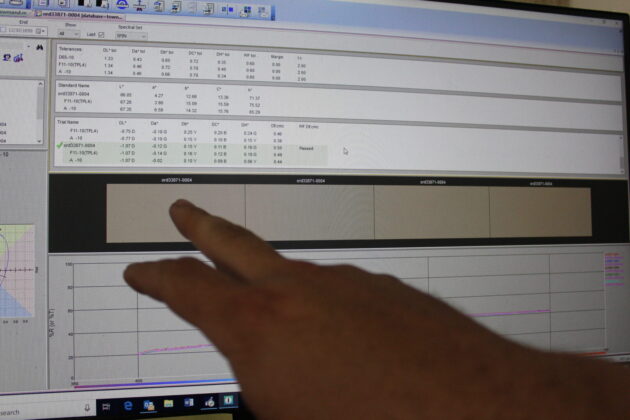
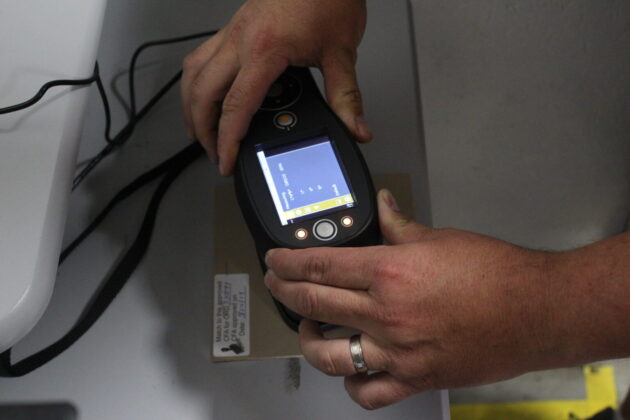
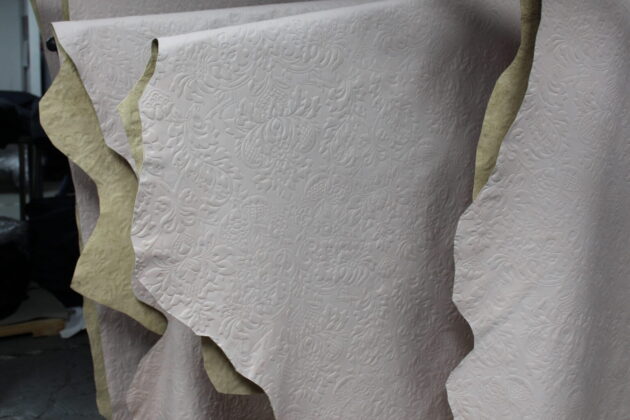
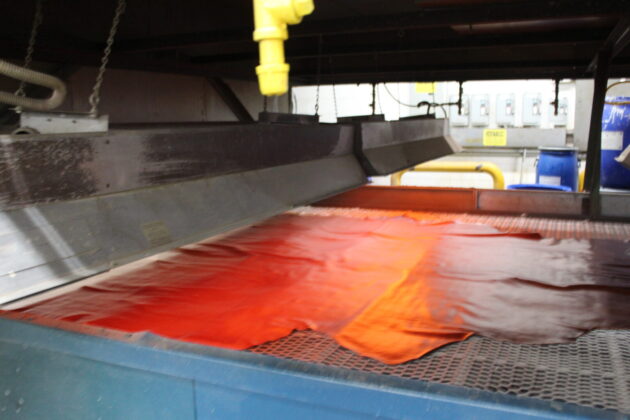
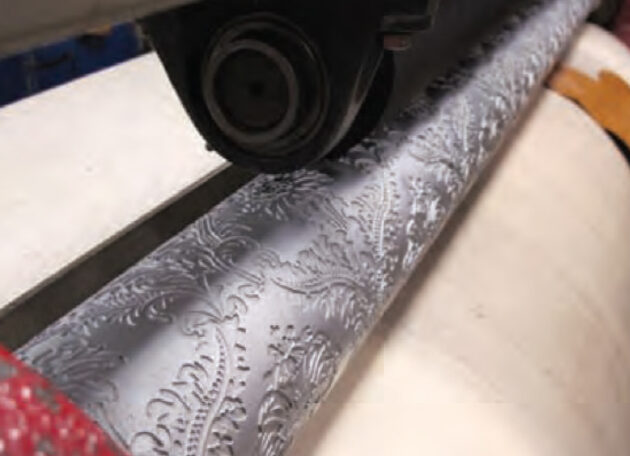
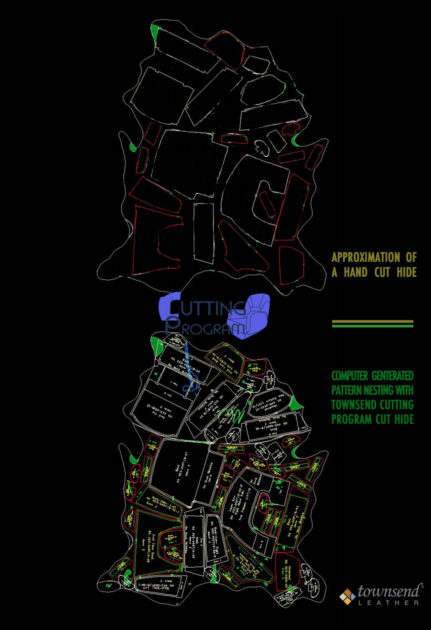
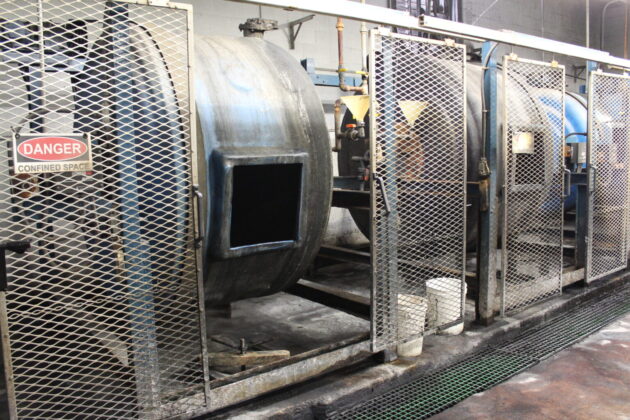
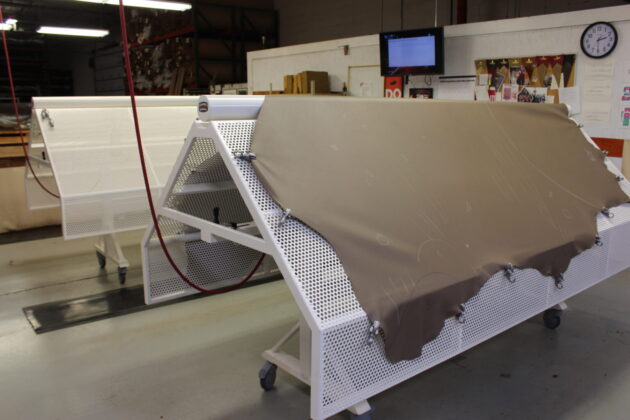
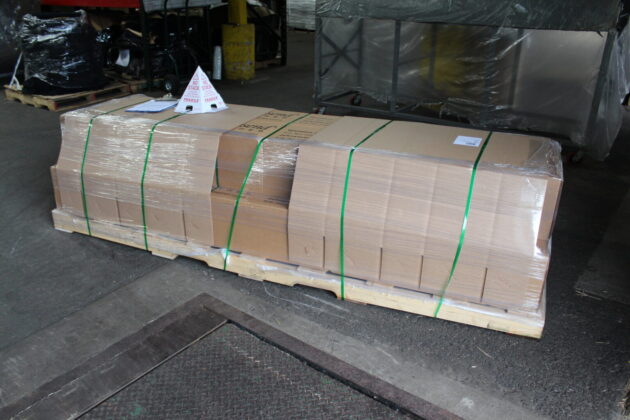
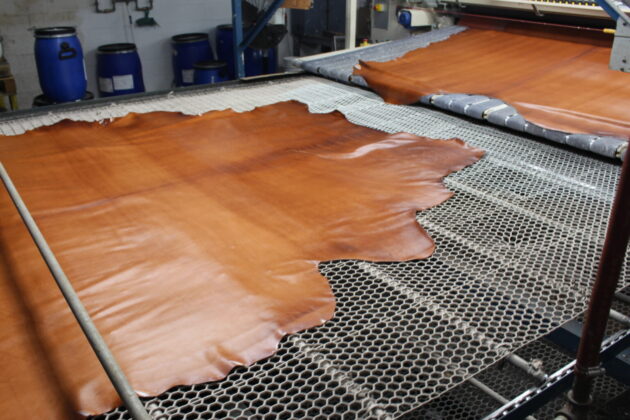
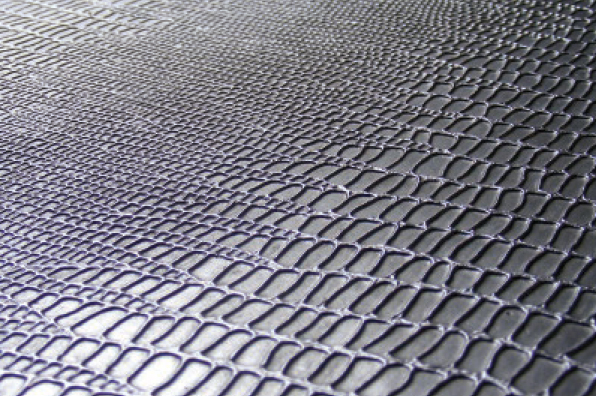
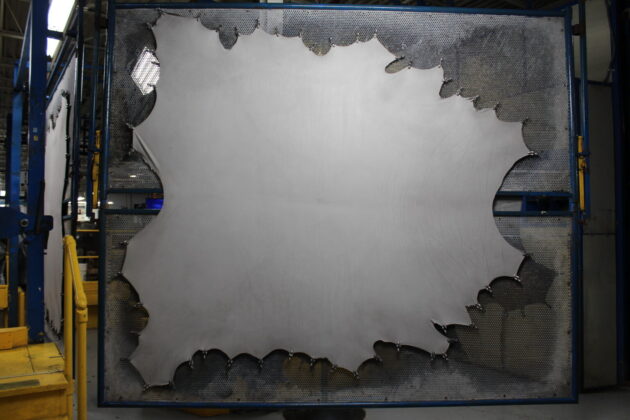
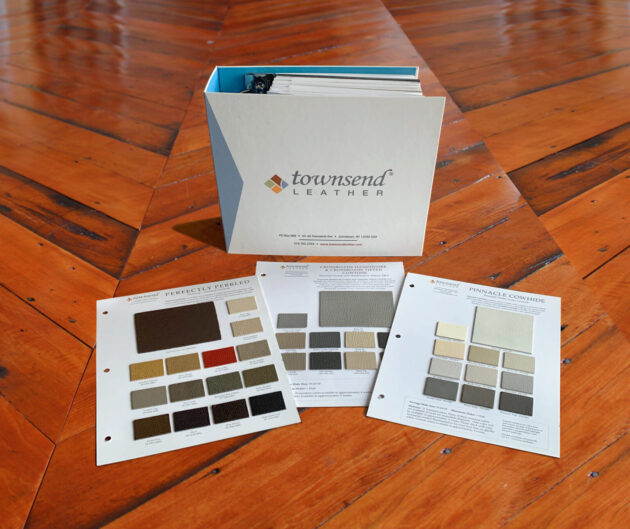
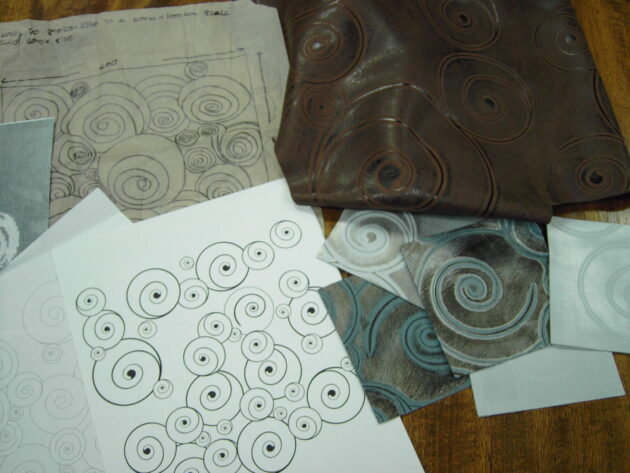
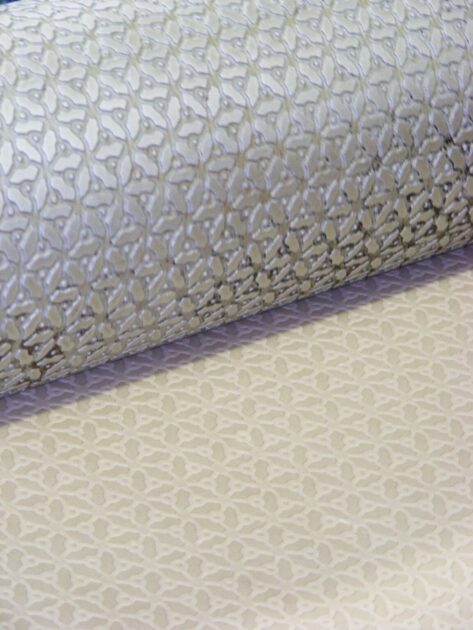
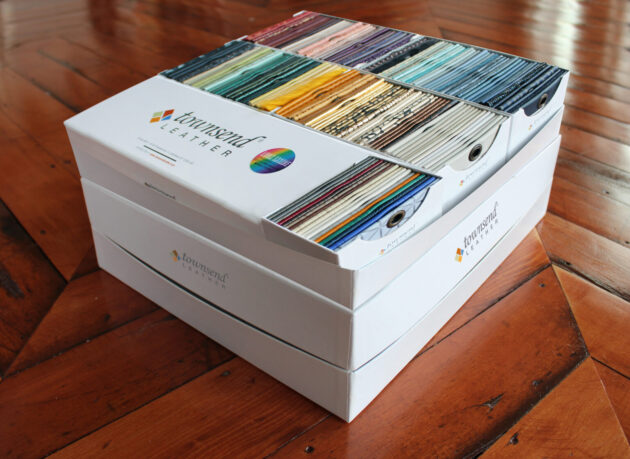
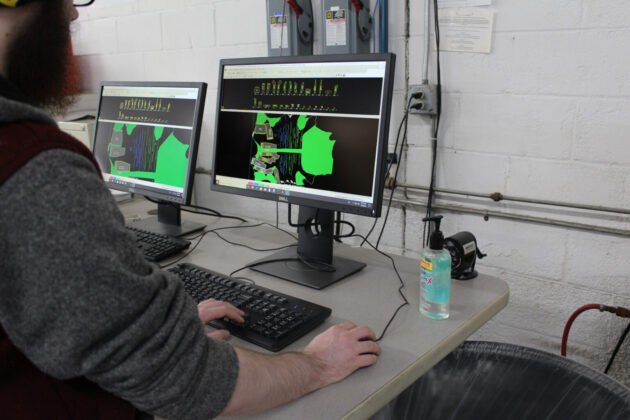
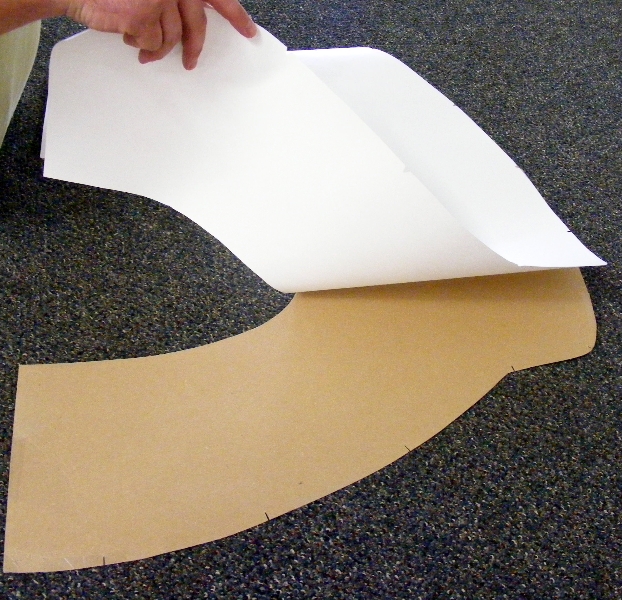
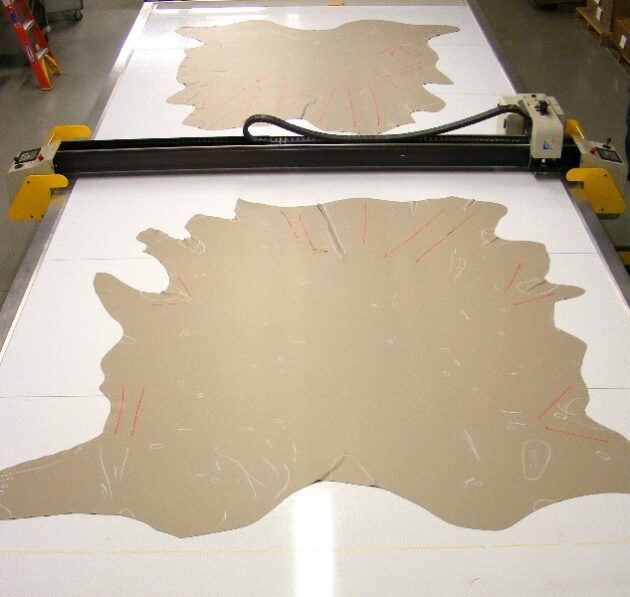
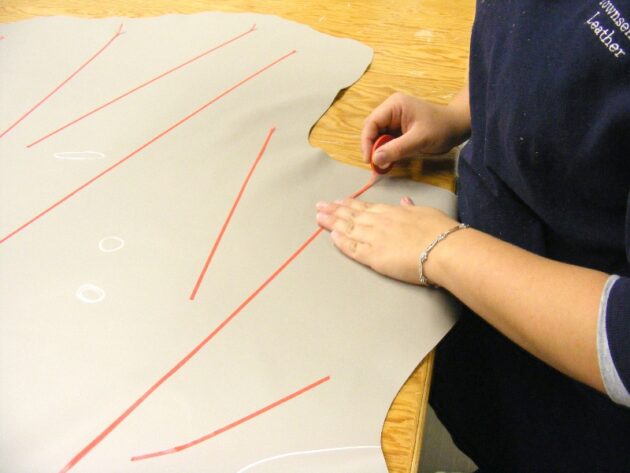
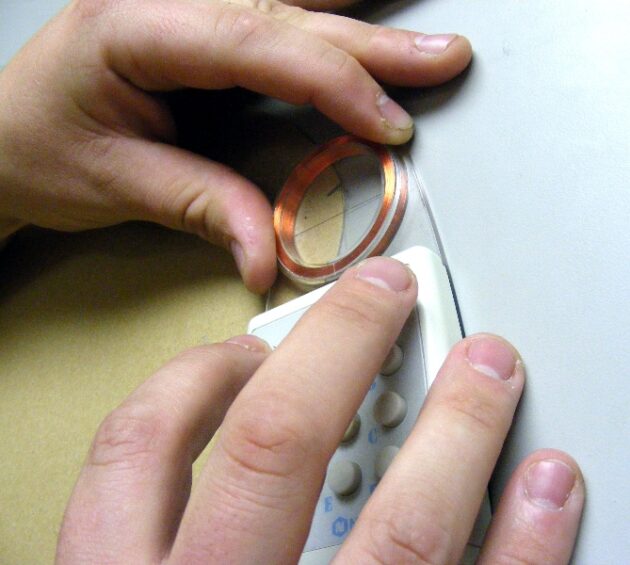
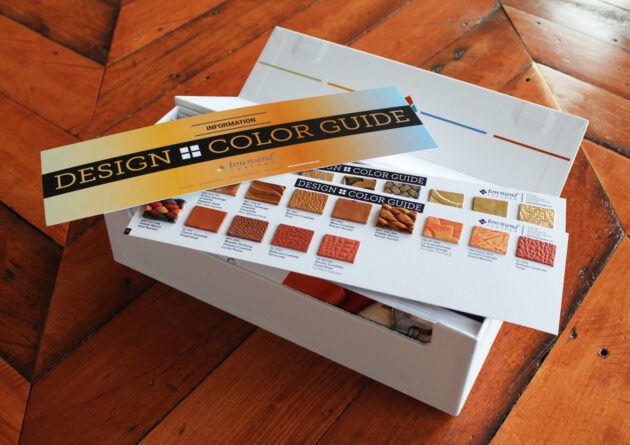
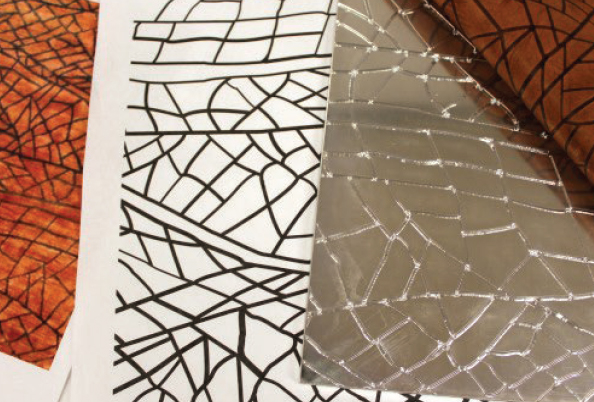
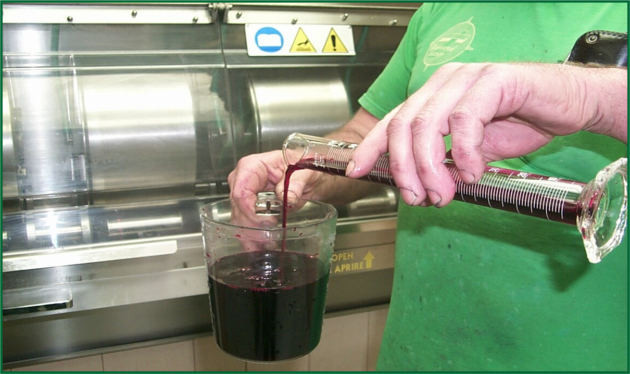
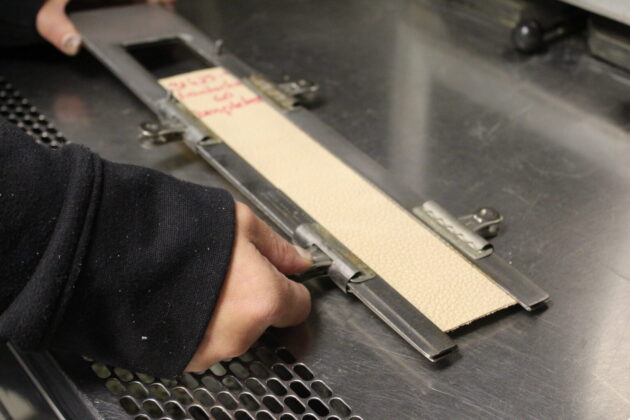
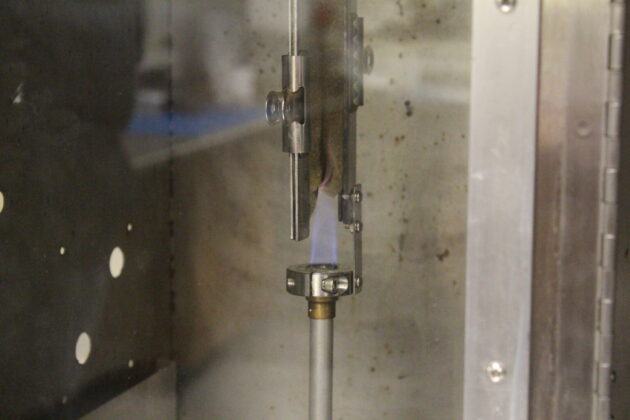
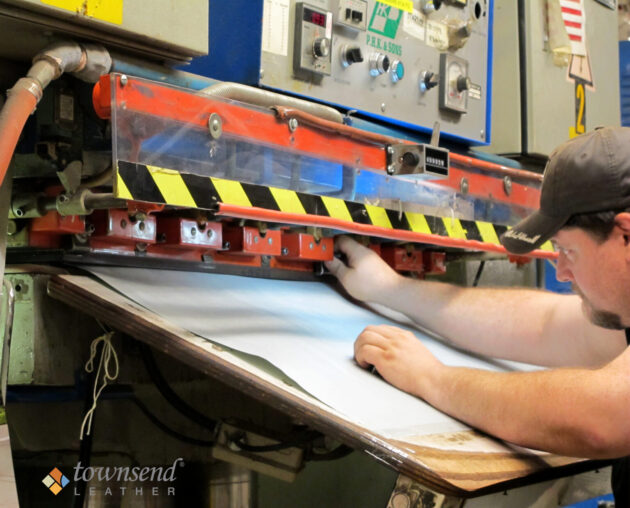
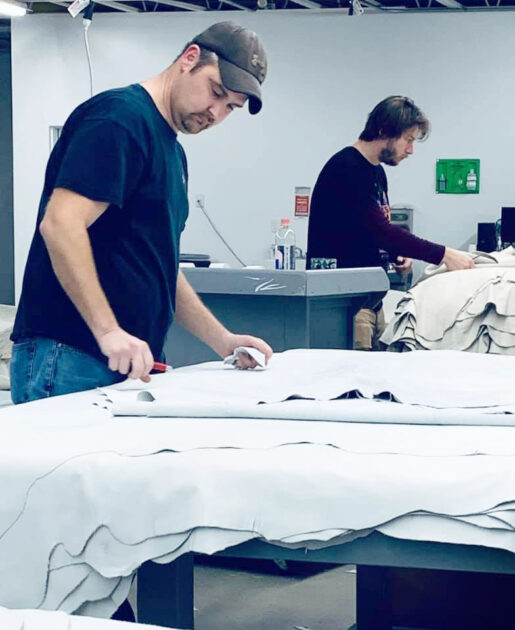
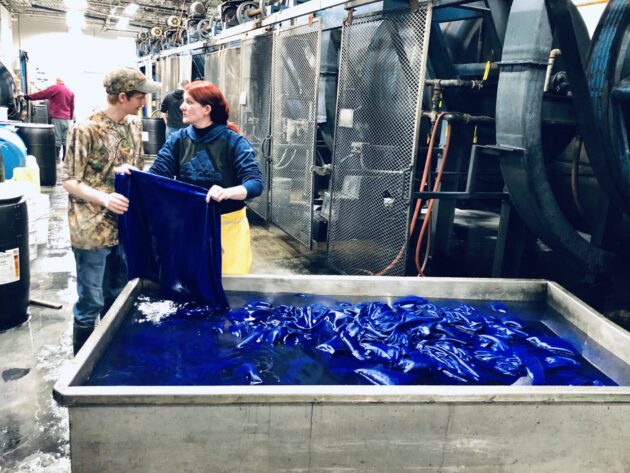
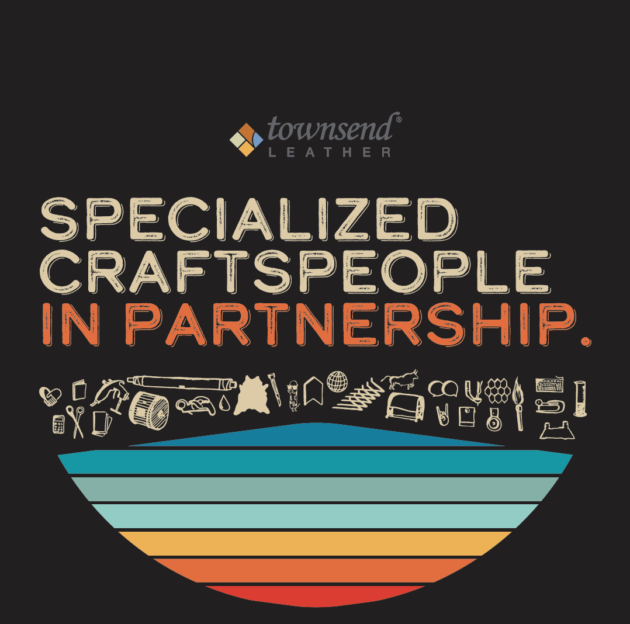
Edit Page
Capabilities
- COLOR MATCHING & CUSTOMIZATION
- EMBOSSING
- PATTERN CUTTING
- QUILTING
- SPECIALTY TECHNIQUES
As the premier manufacturer of fine leather, our team of leather professionals has hundreds of years of collective leather expertise. We are the manufacturer and are driven by a passion for leather, so are always exploring what can be done with leather and can provide leather solutions for any leather dream.
Your leather dream is our dream leather.
Whether it is making the perfect color match or getting the sheen, temper, or feel just right, we can do it. Or maybe you are looking for specialty techniques, one of a kind embossing, or luxurious quilted leather, or performance leather with perforation, or laser etched with your logo, or digitally printed artwork pieces, or patterned foil leathers to enchant the eye, or hand-woven leather, or getting perfectly cut patterns for your large upholstery project… Townsend’s leather capabilities are endless.
For more information on how we can custom craft your leather dream, email info@townsendleather.com.
Open document settingsOpen publish panel
- Page
Color Matching Experts – A Match Made In Leather
With some of the best and most experienced leather color matchers in the world, custom coloring is truly a specialty of Townsend Leather.
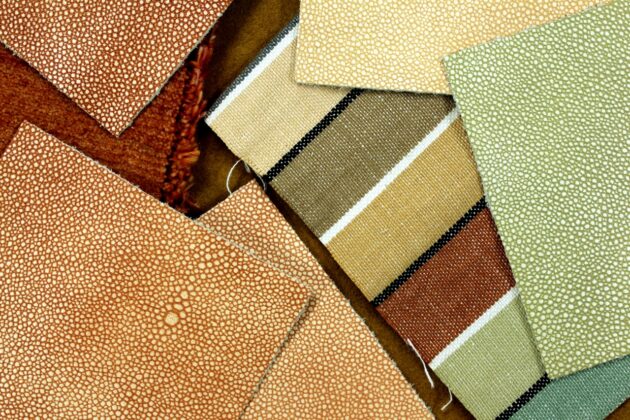
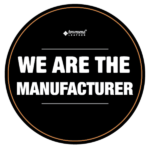
We can match previous dye lots, a swatch, other interior components, or even an intangible concept using our blend of years of color experience and knowledge and the latest technology which results in just the right color you are looking for. We understand the nuances of color, the factors that affect how color is perceived and how to alter color for different effects on different types of leather. We understand that so many design decisions are driven first and foremost by color, and we work closely with our customers to achieve the exact shade, tone, and hue of color needed for each project.
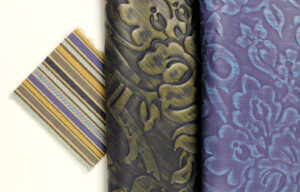
Our Color Matching team takes tremendous pride in being the best in the world for over 40 years at color matching and that is why they chose this simple but powerful statement as their guide and their mission.
Live it.
Love it.
Match it.
A simple message, but one packed with Townsend meaning. Chris Oare worked with his team to craft a Color Matching Department specific Mission statement, and he put his whole heart into, like everything he does.
The Color Matching team’s message encompasses them perfectly. The challenging work they do has to be lived to be done well, it has to be loved to keep doing it, and while the work is matching – the work they do is unmatched across the world.
The live it, love it message is owned and honed by all of the passionate experts on the Color Matching team, but it is one that all Townsend Partners can strive for in all that we do.
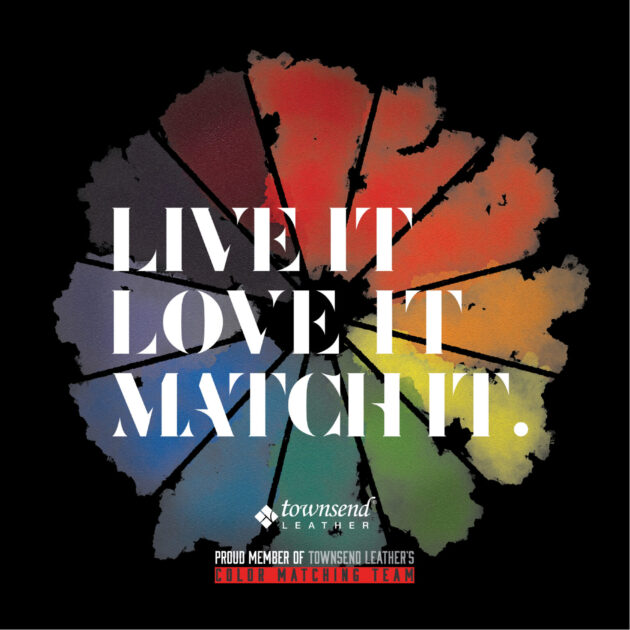
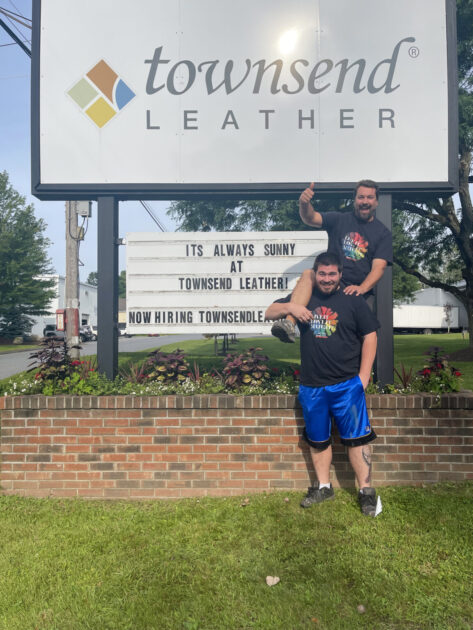
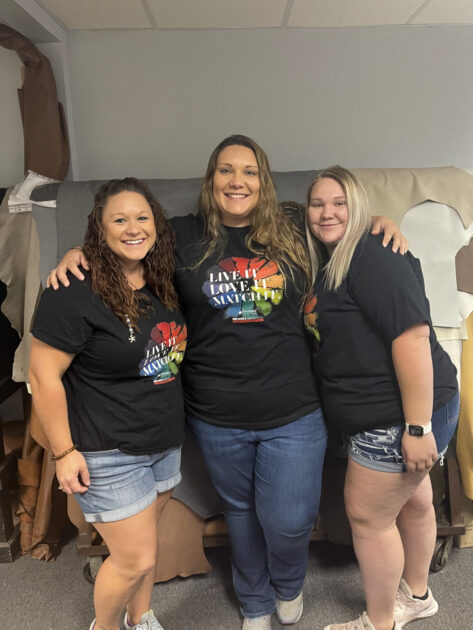
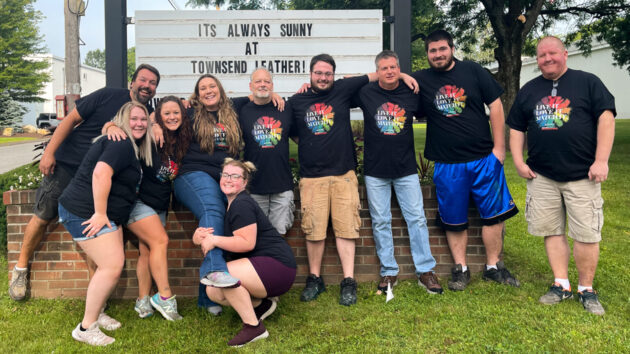
By utilizing hundreds of years of collective leather knowledge, experience, and skill, by combining state-of-the-art technology with time-tested artistry – our Color Matching Team can perfectly match any color you need to perfect your designs. We use the top-of-the-line color reading computer technology and we perfect everything by hand and eye while using light booths to perfect every shade and nuance in every kind of lighting.
There is nothing we can’t match. To really put that idea to the test, as a prank a Townsend Partner once told our Color Matching team that a customer loved the specific color of a road-kill frog and sent it to them in a bag. Without any hesitation, the team just looked at it and said, “which part? the dark areas or the underside that’s kind of preserved…?” Ha! They got right to work on it, until they were told it was a joke. Anything, any color, your dream is our craft – even if it’s a dead frog.
Contact us for details or questions about starting your perfect color-crafting project with us, info@townsendleather.com
Edit Page
EMBOSSING
- COLOR MATCHING & CUSTOMIZATION
- EMBOSSING
- PATTERN CUTTING
- QUILTING
- SPECIALTY TECHNIQUES
Personality. Add it with Townsend Leather.
With our expert craftspeople and campus of manufacturing capabilities, we have endless capabilities to help you see your dreams come to life. We are happy to work with designers to help bring their creative concepts to life. We can work from sketches or photographs to develop virtual renderings, customized tooling of embossing plates, custom colors, and textures. We can match the hue, value, and chroma of any paint chip, carpet or fabric sample, or another available color reference, including Pantone.
One of the places we truly shine is in our unparalleled embossing capability.
Get your hands on embossed samples Embossed & Gaufrage Category
Your site doesn’t include support for the “jetpack/tiled-gallery” block. You can leave this block intact, convert its content to a Custom HTML block, or remove it entirely.
Keep as HTML
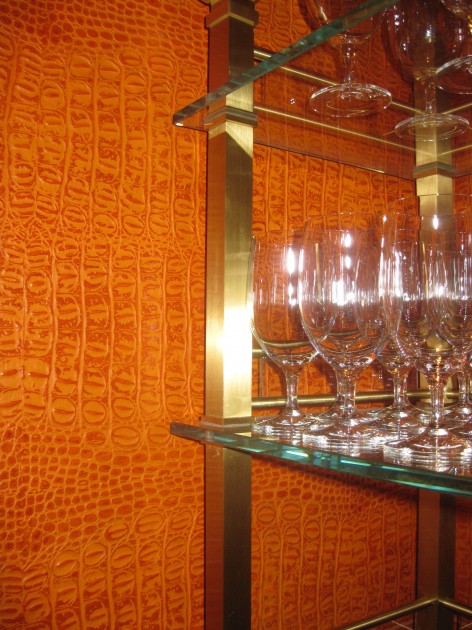
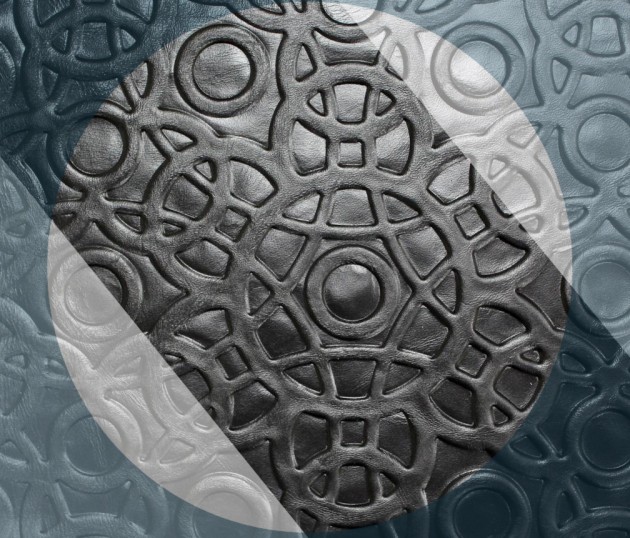
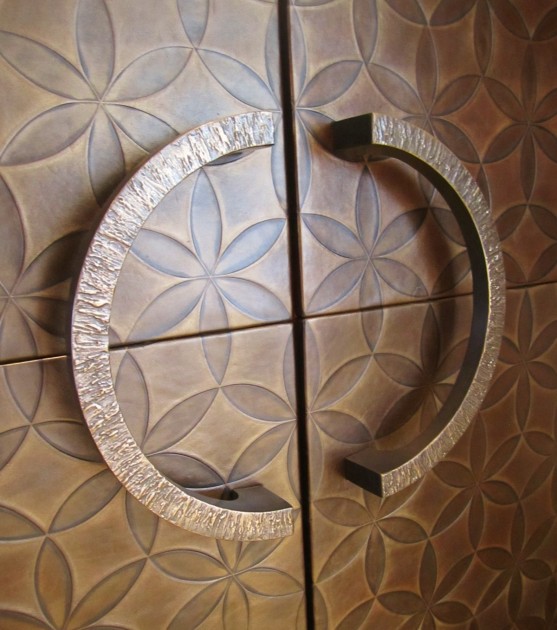
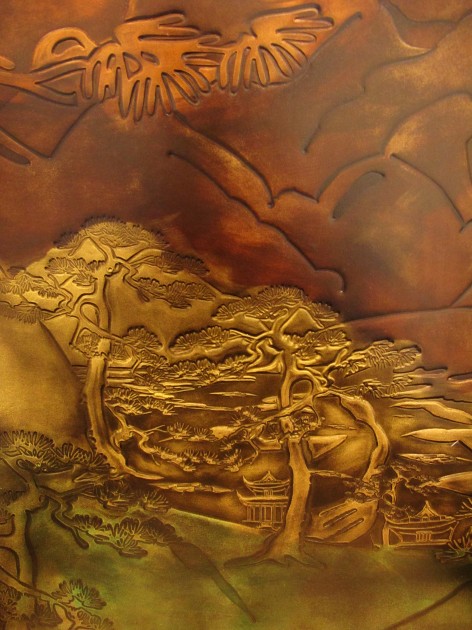
We have the largest collections of embossing patterns for leather under one roof in the U.S. with over 700 embossing plates and more than 140 calendar rolls. Through the use of specialized techniques by our highly skilled leather craftspeople, many textures can be embossed on whole cowhides without showing overlap lines. This maximizes cutting yield and greatly minimizes the need for excess seams during upholstery.
We have internal graphic design capabilities that allow us to create custom embossing patterns in unprecedented turn-around time.
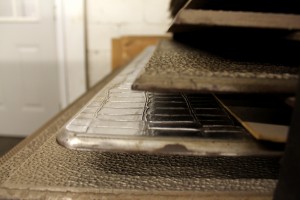
With our extensive library of embossing rolls and plates, and our years of hands-on manufacturing experience, we can help create the leather you envision. Together we can explore all the options available to create that one-of-a-kind look.
Once you have an idea of what you want, and you’re interested in a few test samples, we can quickly produce strike-off samples of custom colors and textures for you. That way you will actually be able to see and touch the leather that was inspired by your vision.
At the heart of Townsend’s creative solutions is a service unique in the industry, one that unites the creativity and vision of the interior designer with the experience, skill, and workmanship of the leather manufacturer. Find out more about our endless embossing capability: info@townsendleather.com
Download
Gaufrage Roller Embossing – Townsend Leather FINAL
Download
Open document settingsOpen publish panel
- Page
If you are looking for savings on yield, time, and cost and you have cut parts and/or repeat patterns to get from your hides – our Cutting Program is a dream solution.
Our high-speed, modular leather cutting system features automated hide scanning, perimeter identification and flaw recognition. It offers the most advanced cutting and nesting technology available today for improving cutting yield and overall productivity.
Contact us to start setting yourself up for savings with Townsend Cutting Program, info@townsendleather.com
For customers with pattern cutting requirements, the Townsend Pattern Cutting System can produce multiple sets cut to your specifications on schedule and at defined costs.
Townsend currently has seat and interior cutting programs with Bombardier, Cessna, Ipeco, and FACC and has also cut for Jet Blue and Embraer. Townsend also produces cut sets for residential and hospitality applications such as headboards, wall coverings, and case goods.
The Townsend Pattern Cutting Systems Advantages:
- Efficiency
- Handling time / Inventory management / Production scheduling
- Maximum Yield
- Reduces Waste / Overage / Scrap
- Significant savings on shipping costs
- Minimizes risk of shipping damage
- Receiving and Storage Savings
- Maximizes Quality Control
- Inspection & Pattern Conformity Ensured
Leather Cutting Program Information
Order Quilted Leather Samples or a full box set of Quilted Samples here: Townsend Leather Quilted Leather Designs
Quilting By Townsend Leather.
You choose the design, we control the quality.
With our on-site customizable quilting machine and expert craftspeople, we can take your dream and stitch it into a beautiful reality of your exact specification. Our AS9100 certification and on-site manufacturing ensures the highest of quality.
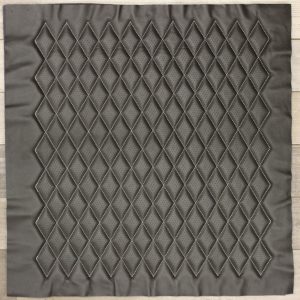
Townsend Leather recently acquired state-of-the-art machinery which allows us to create standard and one-of-a-kind pattern seat inserts and panels featuring decorative patterns made through a combination of technical stitching and custom perforation.
This unique process uses both thread and hole punches to create beautiful, quilted patterns. Quilted Leathers can be produced on any one of Townsend’s In-Stock, standard, or custom-colored leathers and the whole process is completed at Townsend’s Upstate New York facility with quick turn times and attention to the finest quality.
We are generally able to provide customized samples to your specifications but there will be a fee to cover the costs for these. Lead time and cost for samples vary from project to project.
Your Townsend Leather Customer Service rep will be happy to provide a quotation for both sample and production orders, working alongside you on the details of your project.
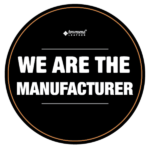
We mean it when we say, we can make your leather dreams come true.
Every technique, every look, every specialty design – we can do it all.
Townsend is the manufacturer, and we strive to have our hands and hearts into everything you can do with leather. So, we have spent decades leaning into ways to create and perfect every specialty design technique.
- Shiny sparkling foiled leathers.
- Specialty and unique skins.
- Incomparable hand-tipping and hand-painted techniques.
- Embroidered leathers.
- Woven leathers.
- Laser etching.
- Perforated.
- Specialty embossing.
- Stencil-crafted.
- Quilted.
- Digitally Printed.
You dream it, we make it.
Contact us, when you are ready to dream your biggest special leather dream.
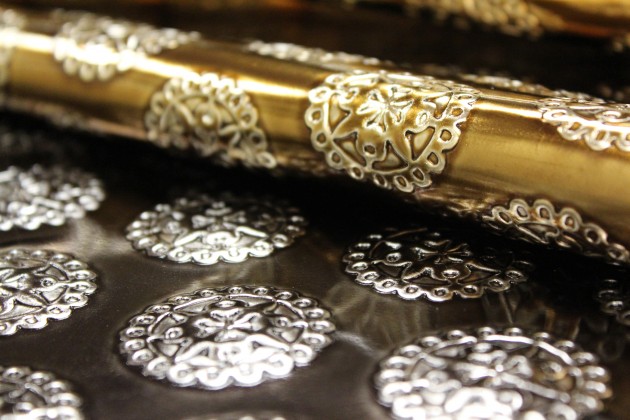
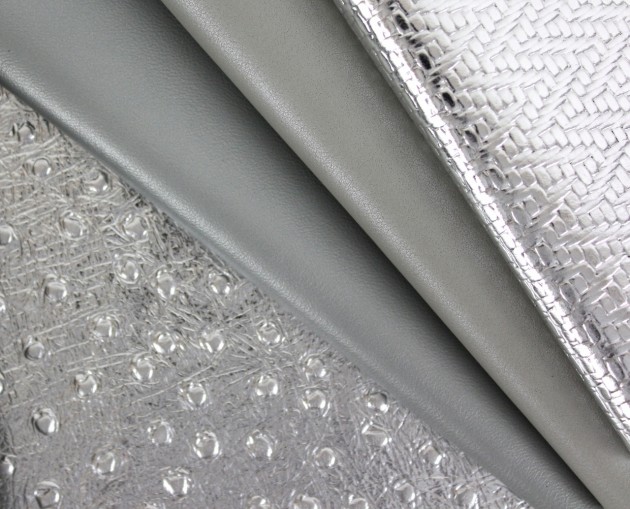
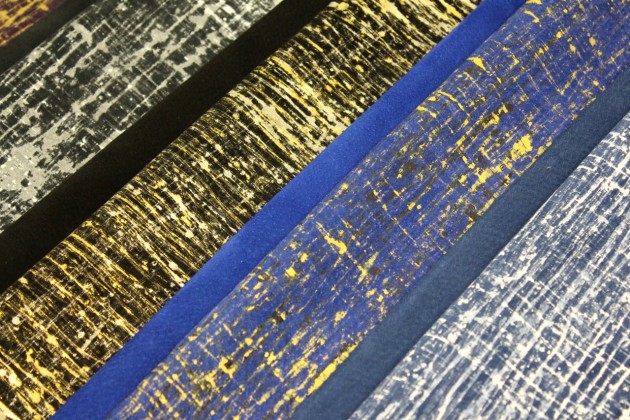
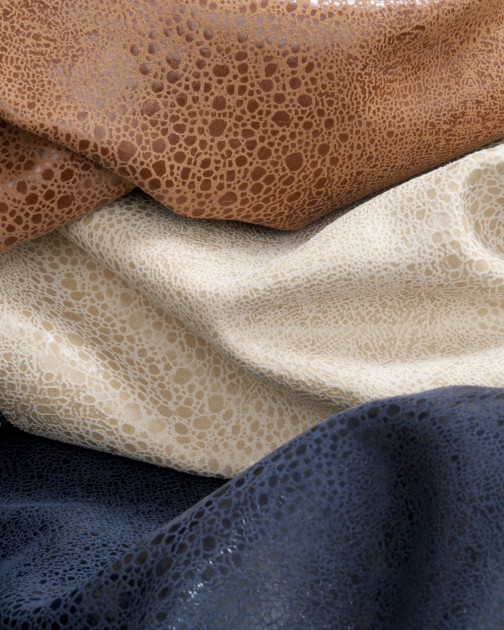
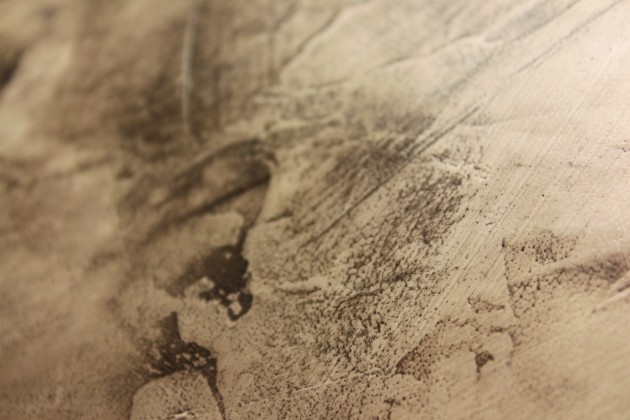
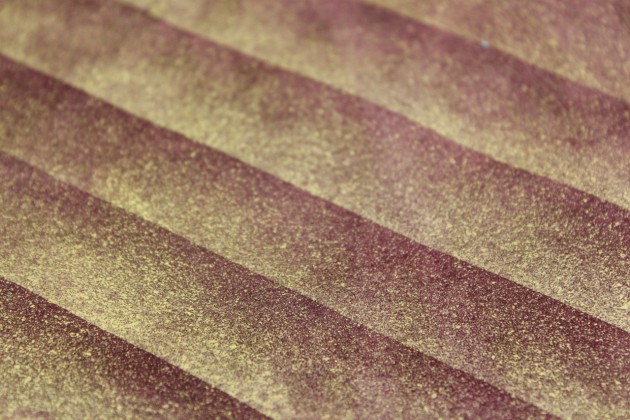
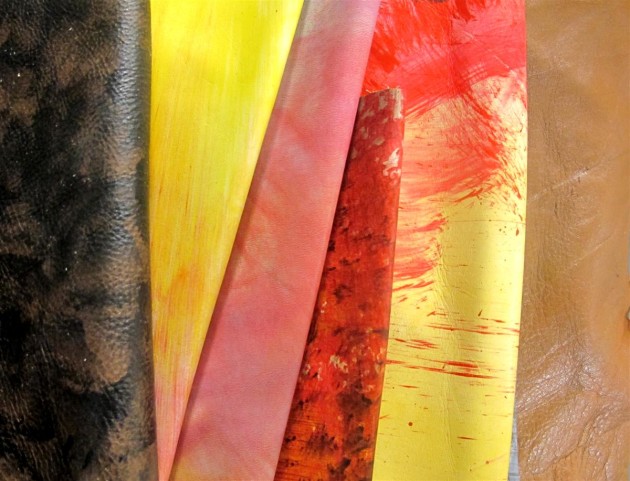
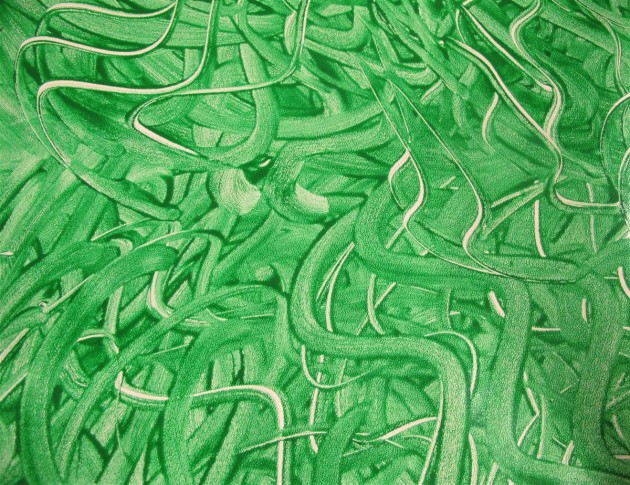
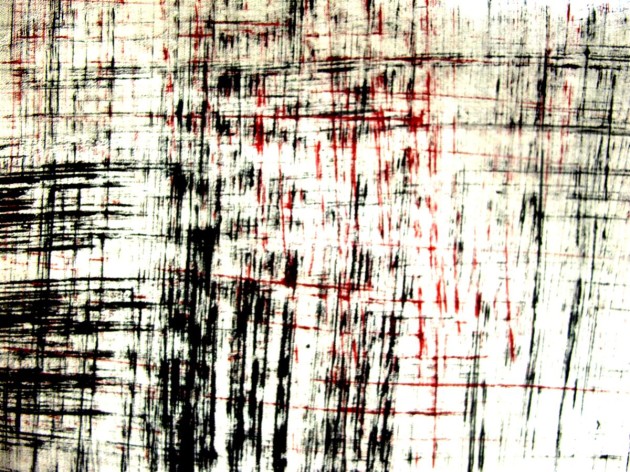
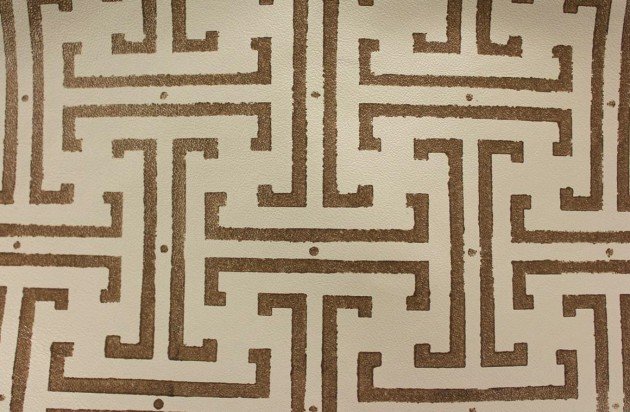
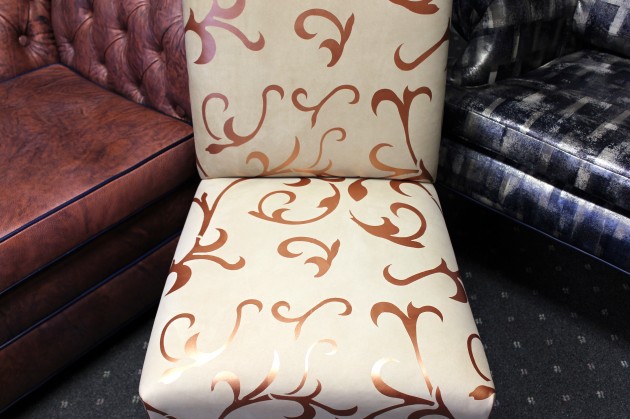
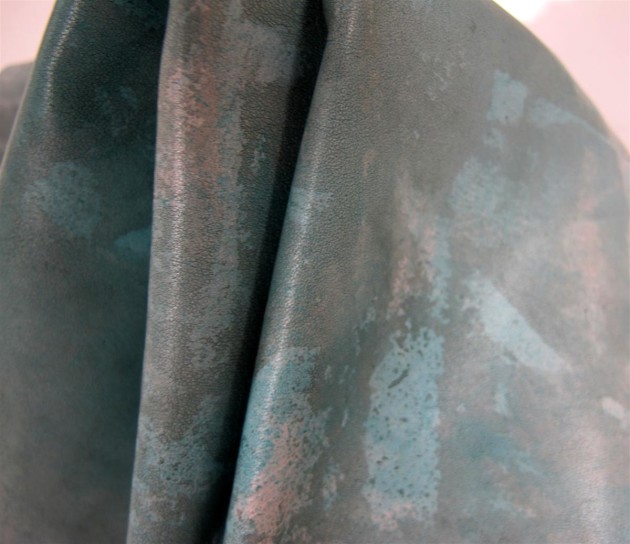
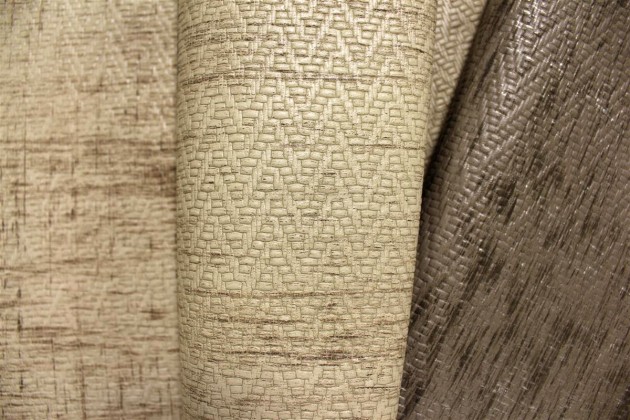
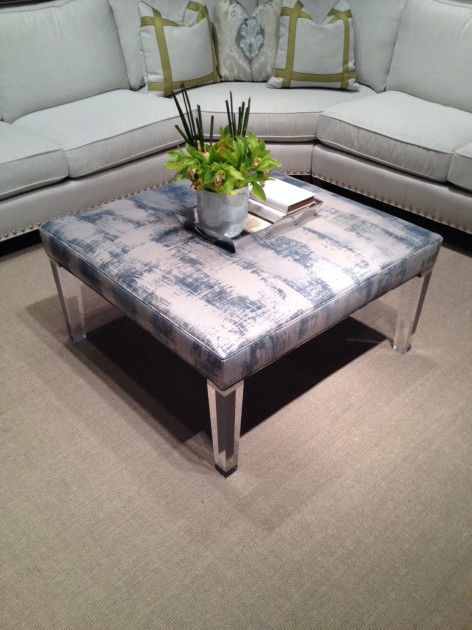
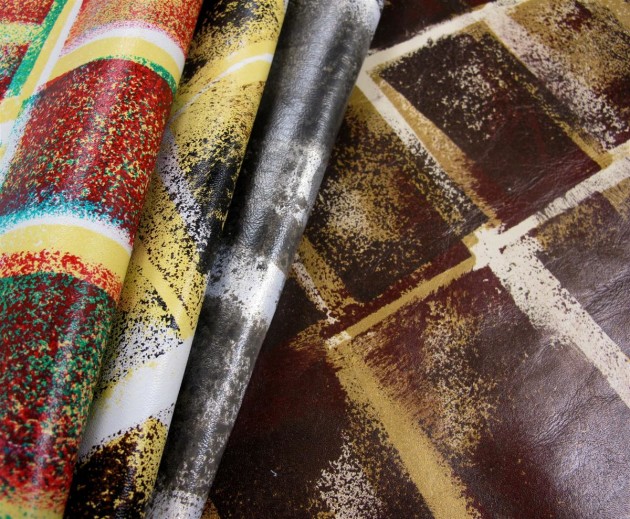
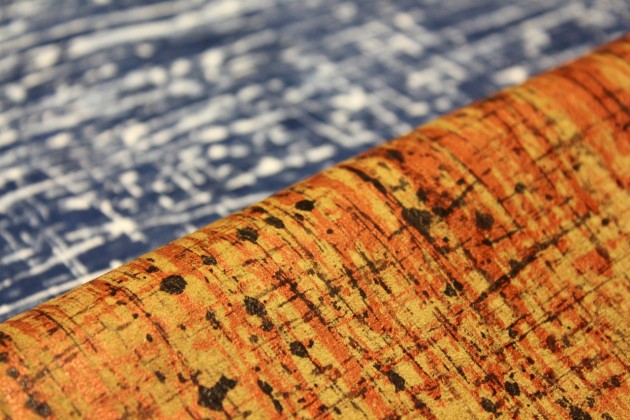
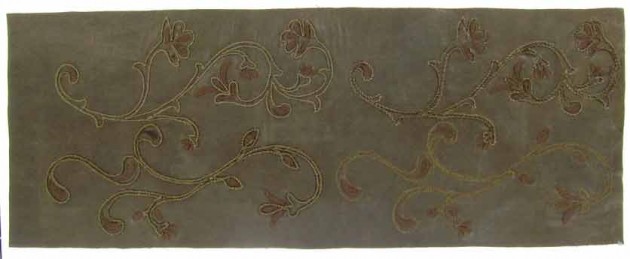
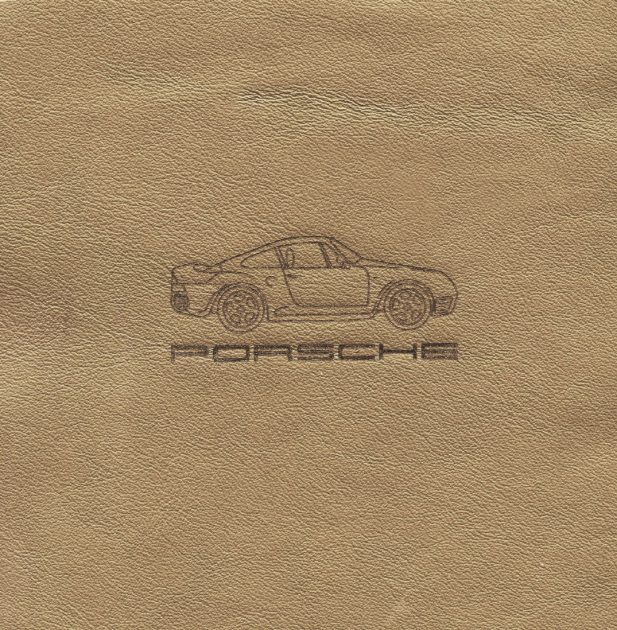
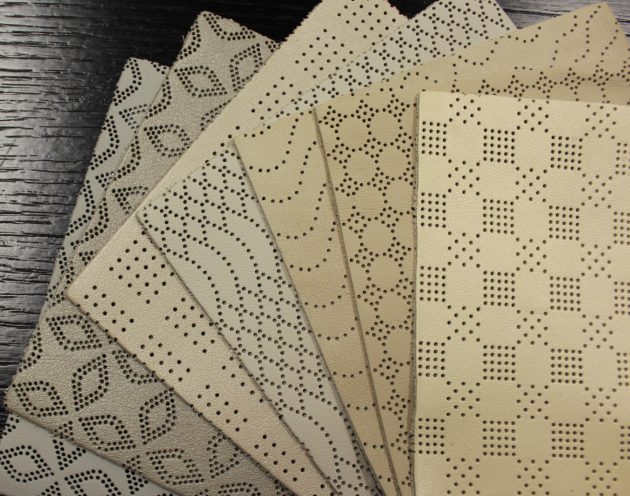
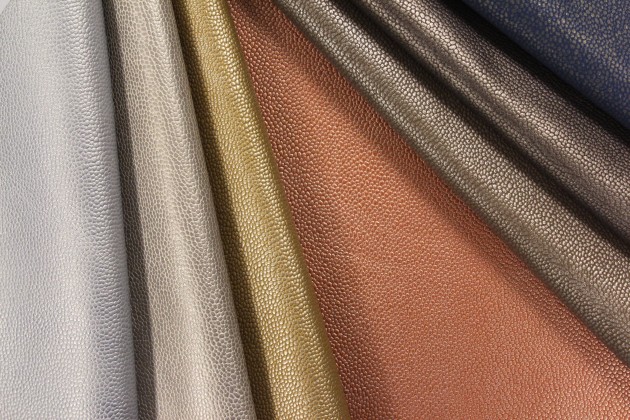
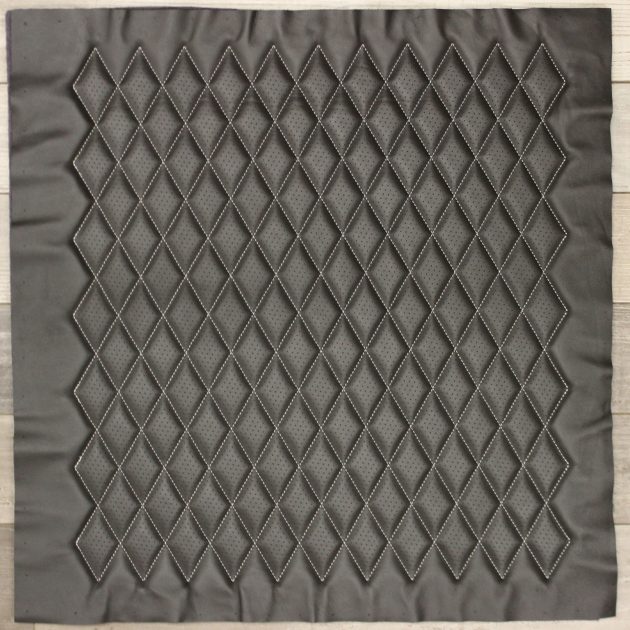
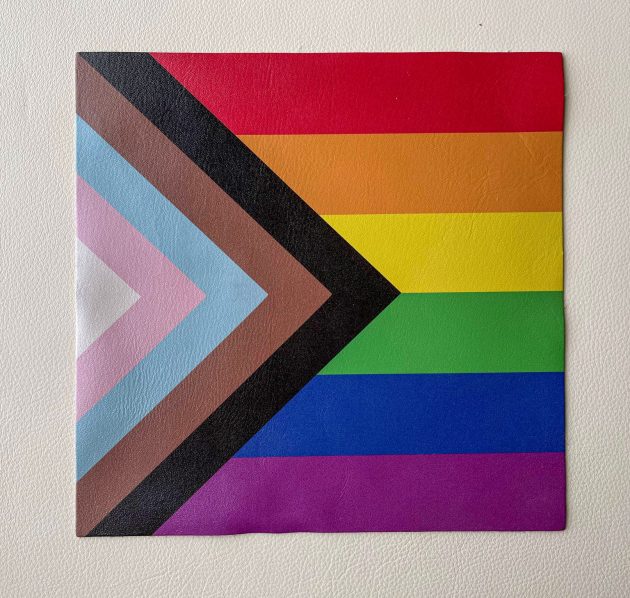
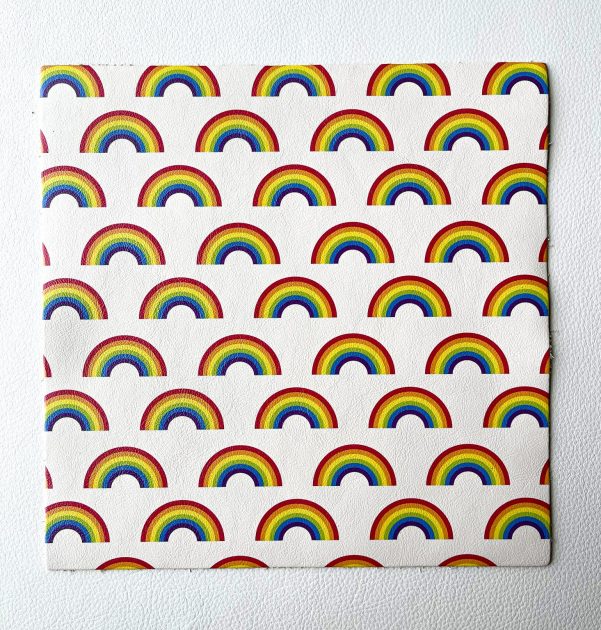
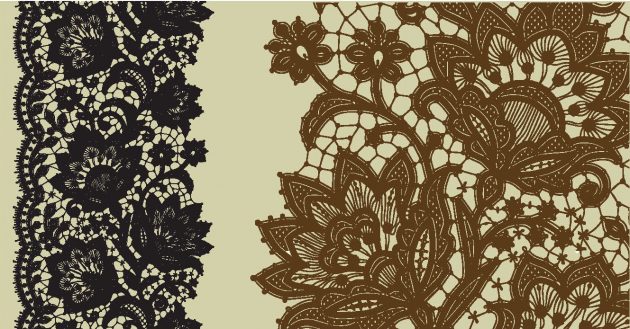
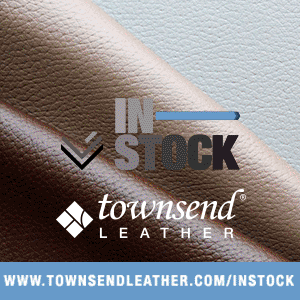
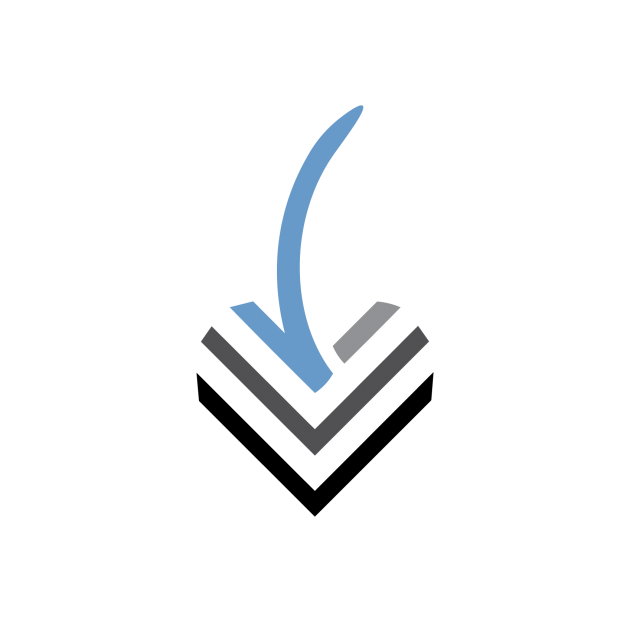
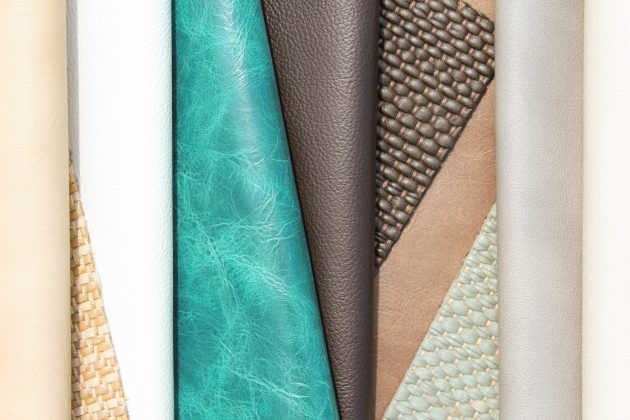
Leathers that give you the time to focus on your love of design.
Townsend Leather understands our client’s desire for innovative and unique products, but also that time is of the essence for many projects these days. Leather is often needed with very quick turn-around times, so we have committed to maintaining stock of the leathers shown here to help alleviate the demands placed on our customers for faster shipments.
Focus on your love of design and check things off your list in confidence with Townsend Leather’s In-Stock leathers.
Townsend Leather is the manufacturer, therefore we control all aspects of the hide production, the dye lot, the quality, the attention to detail. Our In-Stock selection is painstakingly hand-crafted in upstate New York by our leather craftspeople to meet or exceed all our customers’ requirements and our own even more stringent quality expectations, then carefully stored in our custom-built stock department, where the hides are able to retain their natural beauty and shape, ready to be pulled, reinspected, and lovingly shipped at a moment’s notice.
All hides In-stock are flame-treated and meet industry standards for performance and burn certification and are available for immediate shipment or 3-5 business days lead times for Quick-Ship products.
For larger samples or current dye lot cuttings, please contact us.
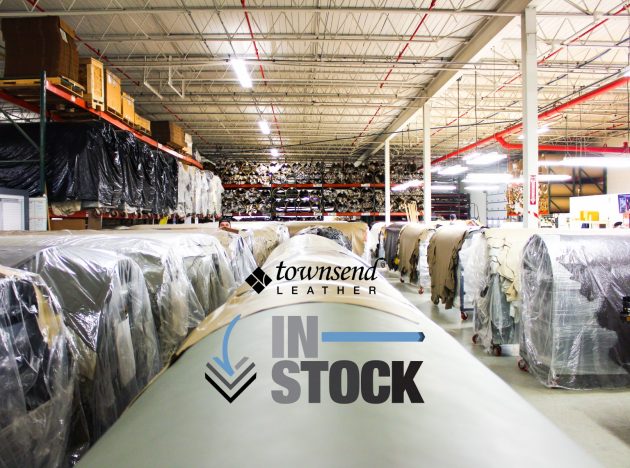